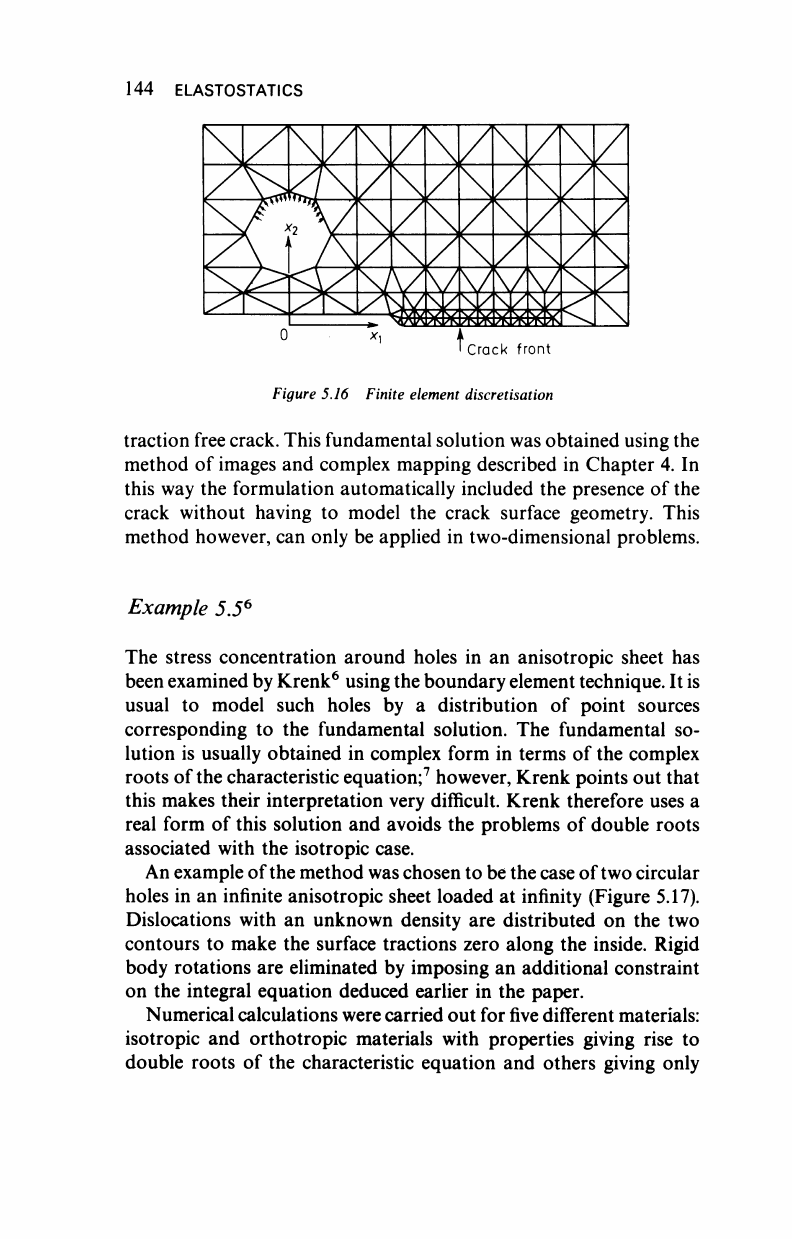
144 ELASTOSTATICS
Figure 5.16 Finite element discretisation
traction free crack. This fundamental solution was obtained using the
method of images and complex mapping described in Chapter 4. In
this way the formulation automatically included the presence of the
crack without having to model the crack surface geometry. This
method however, can only be applied in two-dimensional problems.
Example 5.5
6
The stress concentration around holes in an anisotropic sheet has
been examined by Krenk
6
using the boundary element technique. It is
usual to model such holes by a distribution of point sources
corresponding to the fundamental solution. The fundamental so-
lution is usually obtained in complex form in terms of the complex
roots of the characteristic equation;
7
however, Krenk points out that
this makes their interpretation very difficult. Krenk therefore uses a
real form of this solution and avoids the problems of double roots
associated with the isotropic case.
An example of the method was chosen to be the case of two circular
holes in an infinite anisotropic sheet loaded at infinity (Figure 5.17).
Dislocations with an unknown density are distributed on the two
contours to make the surface tractions zero along the inside. Rigid
body rotations are eliminated by imposing an additional constraint
on the integral equation deduced earlier in the paper.
Numerical calculations were carried out for five different materials:
isotropic and orthotropic materials with properties giving rise to
double roots of the characteristic equation and others giving only