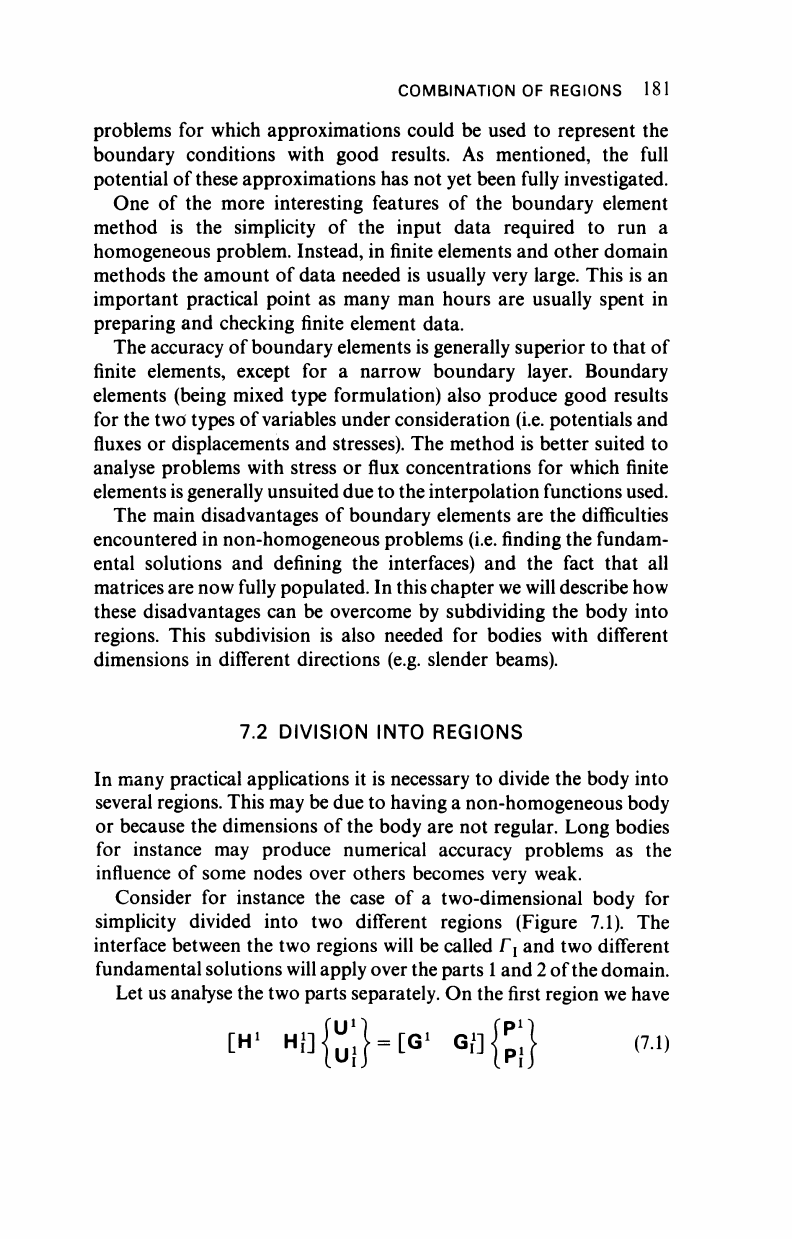
COMBINATION OF REGIONS 181
problems for which approximations could be used to represent the
boundary conditions with good results. As mentioned, the full
potential of these approximations has not yet been fully investigated.
One of the more interesting features of the boundary element
method is the simplicity of the input data required to run a
homogeneous problem. Instead, in finite elements and other domain
methods the amount of data needed is usually very large. This is an
important practical point as many man hours are usually spent in
preparing and checking finite element data.
The accuracy of boundary elements is generally superior to that of
finite elements, except for a narrow boundary layer. Boundary
elements (being mixed type formulation) also produce good results
for the two types of variables under consideration (i.e. potentials and
fluxes or displacements and stresses). The method is better suited to
analyse problems with stress or flux concentrations for which finite
elements is generally unsuited due to the interpolation functions used.
The main disadvantages of boundary elements are the difficulties
encountered in non-homogeneous problems (i.e. finding the fundam-
ental solutions and defining the interfaces) and the fact that all
matrices are now fully populated. In this chapter we will describe how
these disadvantages can be overcome by subdividing the body into
regions. This subdivision is also needed for bodies with different
dimensions in different directions (e.g. slender beams).
7.2 DIVISION INTO REGIONS
In many practical applications it is necessary to divide the body into
several regions. This may be due to having a non-homogeneous body
or because the dimensions of the body are not regular. Long bodies
for instance may produce numerical accuracy problems as the
influence of some nodes over others becomes very weak.
Consider for instance the case of a two-dimensional body for
simplicity divided into two different regions (Figure 7.1). The
interface between the two regions will be called Γ
γ
and two different
fundamental solutions will apply over the parts
1
and 2 of the domain.
Let us analyse the two parts separately. On the first region we have
[H
1
HnjJJ^-Εβ
1
Qajp!}
(7.1)